Although customers might not be able to see the inner workings of your warehouse, their demands for speed, accuracy and timeliness are more keenly felt than ever before. So, it’s up to warehouse managers to make sure that the elements that are invisible to customers remain behind the curtain.
Smart warehousing is one way of achieving greater control and visibility over your stock levels, allowing you to keep operations up and running, fulfil orders and make sure your customers’ purchases are the only thing they’re seeing.
Below, we’ll look at smart warehousing in more detail, including how it can benefit your stock control, some top tips for introducing it into your operations, and how having ‘anywhere, anytime’ visibility across your warehouse can create some real advantages for you and your team.
What is a smart warehouse?
Much like smartphones and smart homes, a smart warehouse is designed to make any tasks you’d usually carry out as streamlined and simplified as possible. In a smart warehousing environment, automated and interconnected technologies work in sync, increasing the productivity and efficiency of the warehouse and keeping human errors to a minimum.
Workers in a manual warehouse, for example, might be used to navigating their workplace, list in hand, picking products and loading them into carts, before delivering them to the shipping docks.
With smart warehousing, these orders are received automatically and then confirmed by smart software to check the products’ stock levels. From there, pick-up lists are sent to robot-carts which place the ordered products into containers and deliver them to workers.
The key to enabling this level of smart warehousing entails fully integrating your Warehouse Management System (WMS) into your back-office system. For manufacturers and companies with a production element to their business, a WMS is a necessity.
For companies with light or no production elements to their business, modern ERP (Enterprise Resources Planning) solutions that include fully integrated mobile handheld technologies (like Intact’s Mobile Warehouse Solution (MWS)) and smartphone warehousing platforms, such as Intact Access, can sufficiently meet your requirements of running a smarter warehouse.
The benefits of better stock control
Improved efficiency and productivity
Manual processes are time-consuming and prone to human error, the effects (and costs) of which can soon build up. By digitising these processes, however, stock control software provides far more accurate monitoring of stock which reduces these costly mistakes.
Equipped with these digitised processes, and mobile warehouse tech like barcode scanners or enterprise mobile apps, your staff have more time to spend on higher-value tasks which can boost productivity as a result.
A single view of stock
If you own multiple warehouse locations or even retail locations, then staying abreast of everything stock-wise can be a challenge.
Stock control software makes things less of a task, providing you with a single, live view of your stock and sales. This lets you correctly allocate stock based on location, so your fast-moving products always stay in stock.
This goes both ways too. Since unsold stock takes up space and costs money, it stops you from ordering top sellers. Through your stock management software’s advanced reporting and analytics, identifying daily and monthly trends is easy, letting you identify what you need to order less of and when. Better still, with today’s advance replenishment rules, you can let your system do this for you.
Greater warehouse organisation
Closely related to the above, when you know what is and isn’t selling, you can create a more organised warehouse based on things like seasonality and product popularity.
Compare this with the old method. A business might see empty shelves and add new stock to these areas without any proper strategy behind it. But this is time-consuming and inefficient as it lacks a logical picking order with which to help warehouse staff locate items.
Stock control software, on the other hand, can identify the areas that allow for the fastest picking routes and consolidated stock bays.
Keep customers happy
Each of these benefits combines to create a more efficient service free from confusion, you can ensure that your customers will keep coming back for more. With improved efficiency, in-stock products and simplified returns and exchanges on your side, the whole process becomes a lot less stressful for everyone involved.
Introducing a mobile warehouse environment
If you’re thinking of implementing mobile warehousing into your operations, then you can make the move a lot smoother with the help of these effective tips:
Go for a mobile-equipped warehouse management solution
If your ERP software can’t support a mobile warehouse solution, then it’s worth scoping out one that can. Through modern handheld technology, you can update the information in your ERP system in real-time, without having to miss out on all-important insights along the way. Here’s a quick pointer: our ERP system can.
Put mobile barcode label printing in place
Mobile handheld technology enable your warehouse team to print barcode labels via a remote printer or put into a queue for your label printer allows for simple and quick printing of barcode labels.
Use mobile handheld technology for inventory counting
Manually counting inventory eats into your team’s day, wasting valuable time and creating untold opportunities for human error. Put simply, your staff don’t need the headache.
However, with mobile handheld technology, it’s possible to simplify the inventory counting process so that your numbers stay accurate and up to date at all times. What’s more, you can carry out rolling stock takes which enable you to keep a regular check on stock levels, helping you to identify any discrepancies early on.
Provide your staff with mobile technology
If your warehouse floor staff are still relying on manual processes to carry out many of their tasks, then it may be time to consider equipping them with the right technology e.g. mobile handhelds, smartphones or tablets. Both staff and customers alike will benefit from streamlined processes, improved efficiency and increased profitability.
How ‘anywhere, anytime’ visibility can optimise your warehouse
Offering ‘anywhere, anytime’ visibility, our Intact iQ ERP and Mobile Warehousing Solution (MWS) makes moving to smarter warehousing smooth and simple. And when you can see more of how your warehouse is operating, you can reap the rewards of this improved visibility with ease.
Here’s how…
Real-time data
By connecting to your Intact iQ system, our MWS gives your team access to real-time order status info, which is essential for meeting lead times and dealing with any lags in your order dispatches.
Increased productivity
Without the need to return to their workstation just to enter data, your team’s mobile devices will do the work for them, allowing them to move from one order to the next seamlessly.
Effective stock management
Optimised with handheld devices, rolling stocktakes let you check stock levels so you can identify anomalies before they create any issues. What’s more, such devices can accommodate multiple stocktaking methods, making partial, ad-hoc and ABC stock counting a breeze.
Intuitive interface
Through your ‘point and scan’ devices, the system is good to go with very little training. Plus, by configuring specific interfaces, your team’s devices display only the fields they need to do their jobs.
And thanks to things like clear stock locations, the intuitive interface also helps to reduce human errors; your team can pick, pack and ship goods without having to fill in paperwork or input data.
Faster booking in
Wherever they are on site, your team can book in stock, and make recordings of stock, pallets, and batches, making the booking-in process far easier.
Quick stocktaking
Stock adjustments and counts can be entered at your facility’s bin location. What’s more, you can assign products to specific stock bin locations. When the products arrive, the assigned stock location is automatically displayed on devices, so your staff know where products can be located when they need to track them down.
Remote site access
Remote sites with Wi-Fi network access, such as one main dispatch facility and multiple storage sites, are more common than ever. By implementing MWS at the remote sites, you can control the movement of stock between the remote sites and your main site, all while staying up to date on your current stock levels.
Proper stock control makes all the difference. Looking for more information? Learn how our Intact iQ system can keep you at optimal levels at all times by heading here or getting in touch with us today.
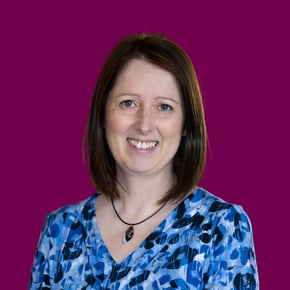